
The effective fabrication duration is reduced to 2 months. Finally, the surface error of ∅1.5 m OAP is better than 1∕50λ RMS (full aperture), and the mid-spatial frequency part is better than 0.64 μrad in slope RMS (effective aperture). We experimentally test this strategy on an ∅1.5 m OAP, as a part of giant steerable science mirror (GSSM) in the Thirty Meter Telescope. In the fine polishing stage, corrective polishing, smoothing, and ion beam figuring are applied in combination to finish. A CCOS-based heterocercal tool is first used in large optics to restrain the edge effects.
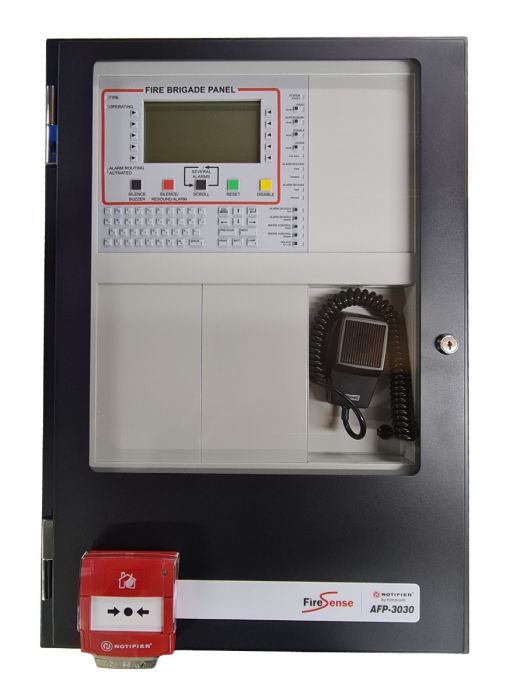

In this paper, we present a large aperture CCOS lap equipped with a compound motion unit and go through the grinding and pre-polishing with its figure errors. However, the fabrication efficiency needs to be promoted in tactical ways. Compared to the stressed mirror polishing, computer-controlled optical surfacing (CCOS) or other computer-controlled subaperture tools provide more flexibility. Off-axis parabolic parts (OAPs) or quasi-OAPs are mostly frequently used in large optical telescopes. © 2018 Society of Photo-Optical Instrumentation Engineers (SPIE).
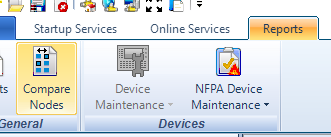
In addition, the results show that the noise level was significantly reduced with the reference sensor even under a high rotational speed. These results confirm that the measurements of the surface form errors were successfully used to modify the cutting tool path during the compensation cut, thereby ensuring that the diamond turning process was more deterministic. An aluminum spherical mirror with a diameter of 300 mm was fabricated, and the resulting measured form error after one compensation cut was decreased to 254 nm in PV and 52 nm in RMS. The accuracy of 109-nm PV and 14-nm RMS was obtained by comparing with the interferometer measurement result. Using the proposed system, the repeatability of 80-nm peak-To-valley (PV) and 8-nm root-mean-square (RMS) was achieved through analyzing four successive measurement results. In addition, a double-sensor measurement was proposed to reduce the electric signal noise during spindle rotation. In the proposed system, a position-Trigger method of measurement was developed to ensure strict correspondence between the measurement points and the measurement data with no intervening time-delay. We present an on-machine measurement system based on capacitive displacement sensors for high-precision optical surfaces. On-machine measurements can improve the form accuracy of optical surfaces in single-point diamond turning applications however, commercially available linear variable differential transformer sensors are inaccurate and can potentially scratch the surface.
